We deliver what no-one else can: we calculate the real Wp
value of each module during operation, in-field.
Simply put: just compare this value to the one at which you bought your modules
– and you can decide about actions to be taken, like warranty claim, cleaning,
etc. SunSniffer gives you precise information about which action is needed –
and if it is economically sensible.
Why is this possible – and how?
Because we measure. We measure MPP, resistance values during normal operation.
By this we see if the modules work as they should or if there is any issue. Our
super low-cost sensor in each module, combined with analysis by artificial
intelligence makes it possible.
Because in laboratories measurements are made under STC conditions
– Standard Test Conditions. Conditions, which will never be found in field.
But the behavior of modules changes with temperature for example. And it changes when connected in a string.
Some issues only appear when certain conditions are
met, like a certain temperature, special shading situation or a particular
string behavior – or any combination; these will not be detected in lab.
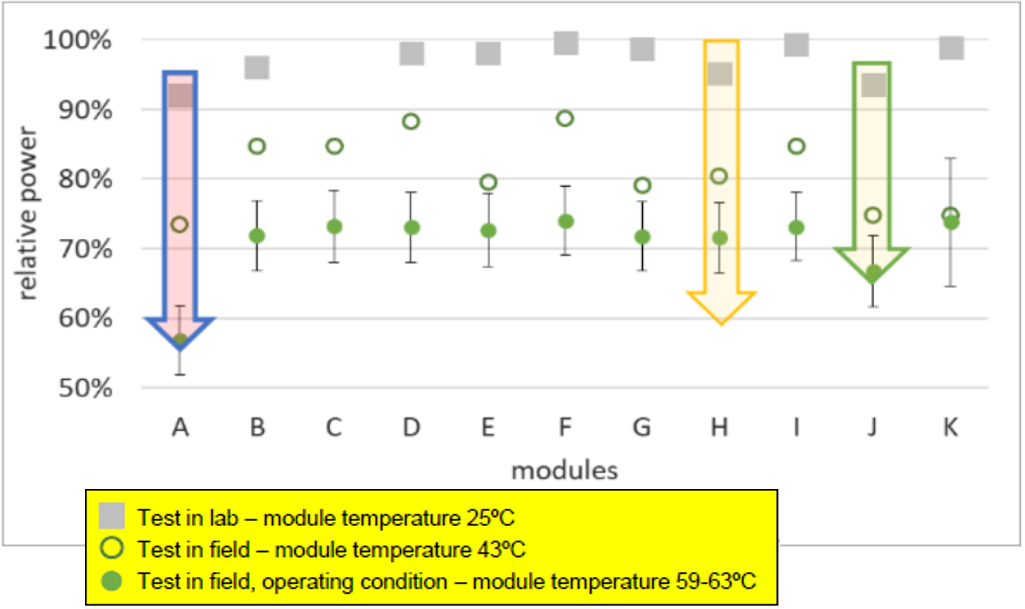
Some errors expose only at a certain temperature. Module
temperature in lab is significantly different to temperature in the field.
Why is voltage measurement essential?
Because current measurements depend on irradiation. Voltage
almost always remains the same; this makes it the perfect base for analytics.
Only influence is temperature, but deviation from temperature is being compensated.
Why is voltage measurement needed at the module, ain’t
measuring string voltage enough?
No, because one defective string reduces the voltage of all
connected strings. So you might know that there is an issue, but you don’t know
which string has it. If the voltage of each module is measured you can pinpoint
exactly the issue.
If you have string measurements, and even if you have artificial intelligence
analyzing it, you always need further tools in addition, like drone flights, to
exactly localize the issue.
There are other methods for testing in-field, established
methods; ain’t that enough?
No. Because these measurements are not precise enough;
infrared for example cannot detect losses below 8%, according to a ZAE study. Every issue below 8% remains undetected, adding up huge losses over
time – and being not even noticed!
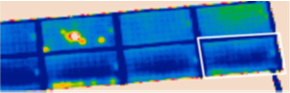
Some errors even remain invisible in field checks. Module in
white frame is not striking in the thermal inspection, but suffers from 2,9%
power loss.
So what exactly are the benefits of SunSniffer?
► We detect low-level, creeping losses, like PID, LID, LeTID.
► We detect any newly appearing power reducing issues of new materials/technologies/etc.
► We monitor – and analyze – the whole plant down to each module, constantly, during normal operation. Any deviation is detected instantly.
► We sort the modules into loss classes: modules can be cost-savingly exchanged in bundles.
► We facilitate warranty claims: generate a performance report of any module at any time just at the push of a button and send it to your manufacturer.
► We offer precise ROI calculations: for asset management, for investors, for insurances, for sale options, etc.
► We offer comprehensive fault management tools for easy, fast and cost-effective O&M.
► We offer different information levels, for asset manager/utilities, for home owners, and for scientists.
► SunSniffer doesn’t even cost more than any other monitoring solution!
SunSniffer = combination of precise measurements +
internet-of-things + artificial intelligence.