Whole plant at a glance? With SunSniffer®'s "Deep View" the functionality of each module is visible...
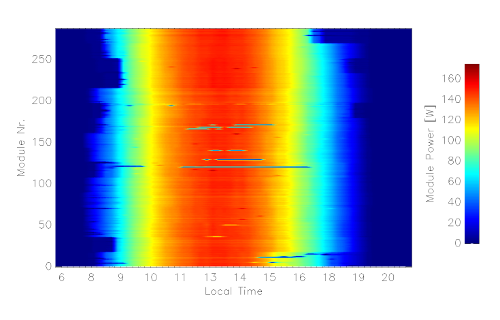
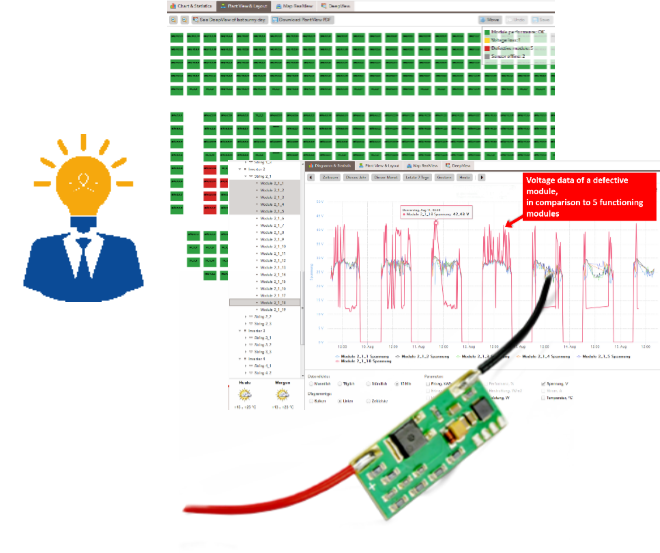
The biggest problem with PV plants: They may work, but you can never be sure how well. Power reducing errors - if noticed at all - must be searched, and this is time-consuming and expensive. In this way the operators not only loose yield, but the error-finding produces costs as well.
SunSniffer is different: we monitor the whole plant, including each single module! Without module monitoring you have no other option than visit the plant on-site in order to identify problems. Those plant inspections require appropriate weather conditions, appropriate qualification and equipment of the technician, etc
Our innovation is a pioneering technology. It lowers the major cost factors in the operation of a plant - maintenance, error detection and fault finding - and ensures through the continuous real-time monitoring of each module for a constant and optimal energy production and, even, increase. It is much cheaper than so-called "optimizers" and offers far more applications, safety and comfort. There is no comparable technology anywhere in the world. It is protected by patents in numerous countries worldwide and originates in Germany
Internet of Things
Our technology has heralded the Internet of Things in photovoltaics. "Monitoring 2.0" means: data ANALYSIS and the provision of clear instructions for non-techies. It means: finding each black sheep among the modules! This is exactly what our "SunSniffer®" is capable of. Allying a simulation engine with artificial intelligence, based on Big Data and a NoSQL database with unlimited data processing capacity enables the module to accurately detect and define not only errors, but also error patterns. So, at a glance and in real time, you are able, via our web portal remote monitoring, to see which module has which problem - and what needs to be done. It is no longer necessary to send an expensive technician for more time-consuming, and often inaccurate (!), troubleshooting. Nothing could be clearer or more simple. And our system is so brilliantly simple that the hardware costs are less than 1 cent / Wp* – which corresponds to one single IR-thermography of the plant, whereas we check all modules every minute.
* Depending on the size of a plant
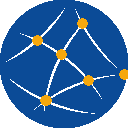